Insulin
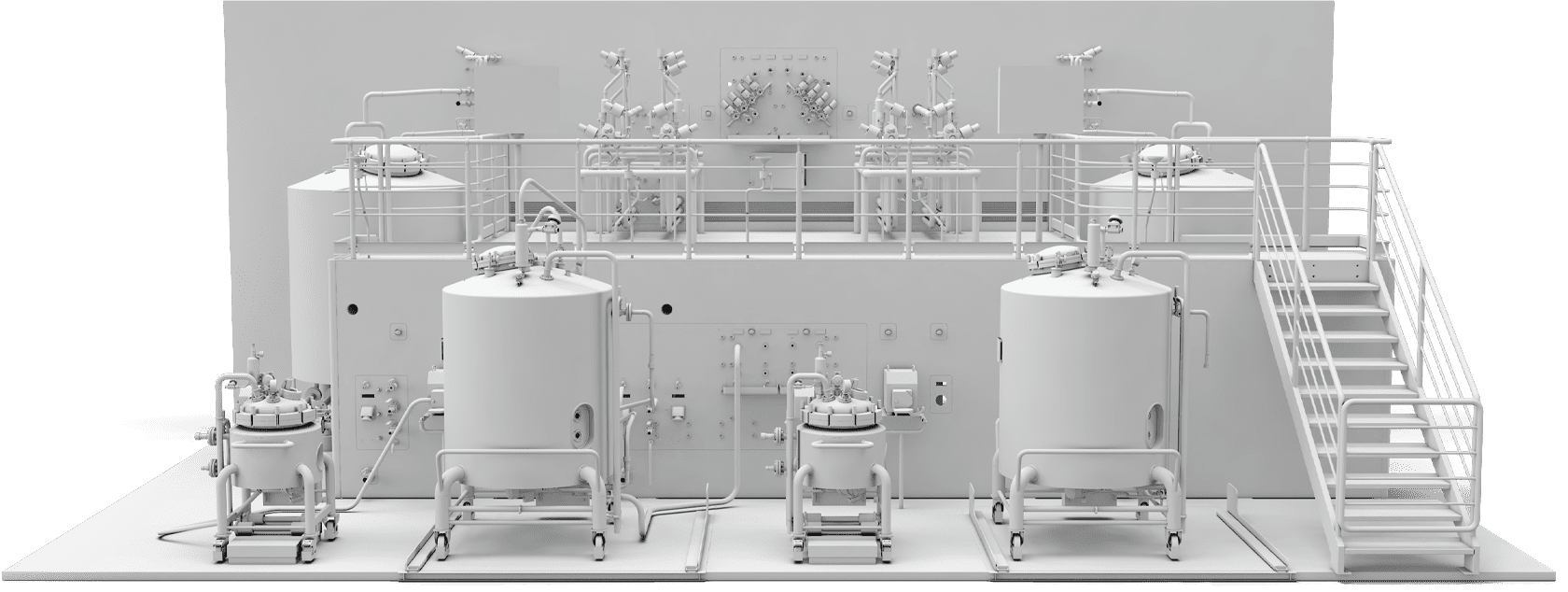
Sterile formulation project
-
Overpressure group and back of transfer panel
The mechanical components behind a flawless process
-
Sterile transfer panel
To transfer fluids safely and without losing sterility
-
Sterile Filtration Unit
Absolute hydrophilic filters to maximize filtration process for polar liquids – 0,45 pre-filter and 0,22 sterilizing filter
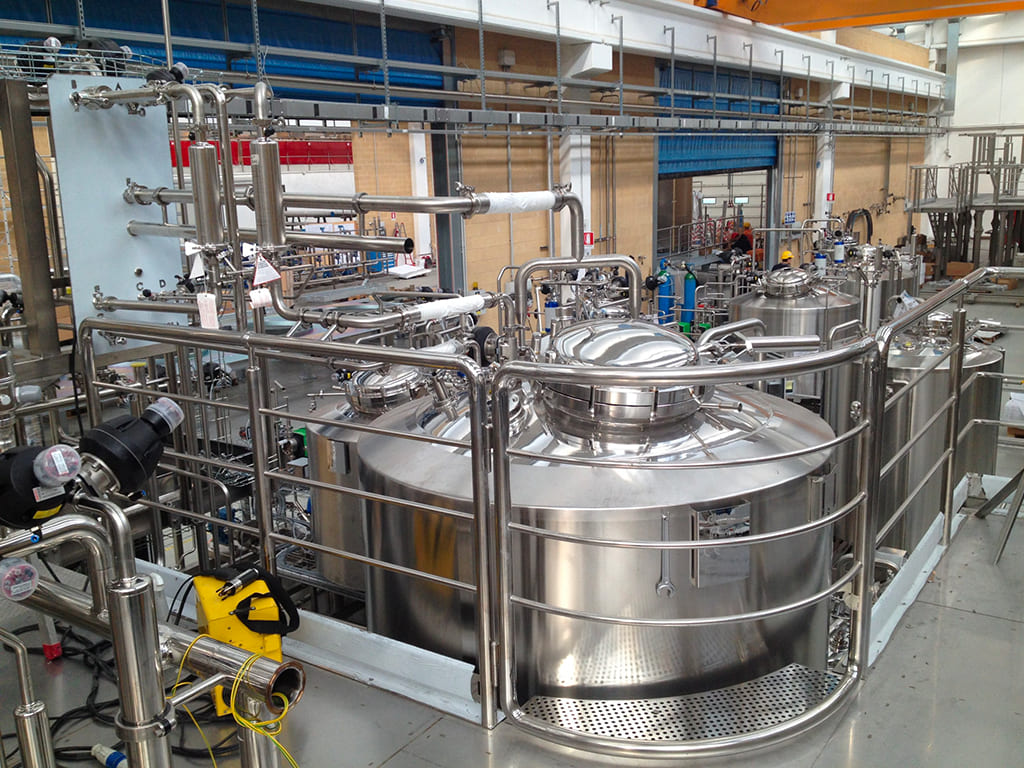
-
Complete Solutions
Designing and building an insulin plant is not a breeze: the plant has to follow cutting-edge technologies and be managed with sophisticated automation systems to implement process phases and to obtain a product to be classified as sterile.
The partnership with one of the largest Pharma Company, specialized in diabetes care, has been written in stone thanks to almost 10 insulin plants developed in 15 years.
The insulin market is constantly growing and so it does manufacturers’ need of production. These plants indeed are one of the most required: more than 450 million adults (20-79 years) lives with diabetes; prediction says by 2045 this number will rise to 700 million (International Diabetes Federation).
-
Explore
Biosynthetic production of human insulin is often done using bacteria, whose fermentation starts in culture broth.
The lispro insulin produced in this plant with recombinant DNA technology is very much similar to the hormone produced by Beta cells of human pancreas. The synthetic insulin differs just in a short part of its structure which makes possible a faster absorption and effect.
Lispro insulin can be administered by subcutaneous injection and by continuous subcutaneous infusion through external pump. In case of emergency, the drug may also be administered intravenously.
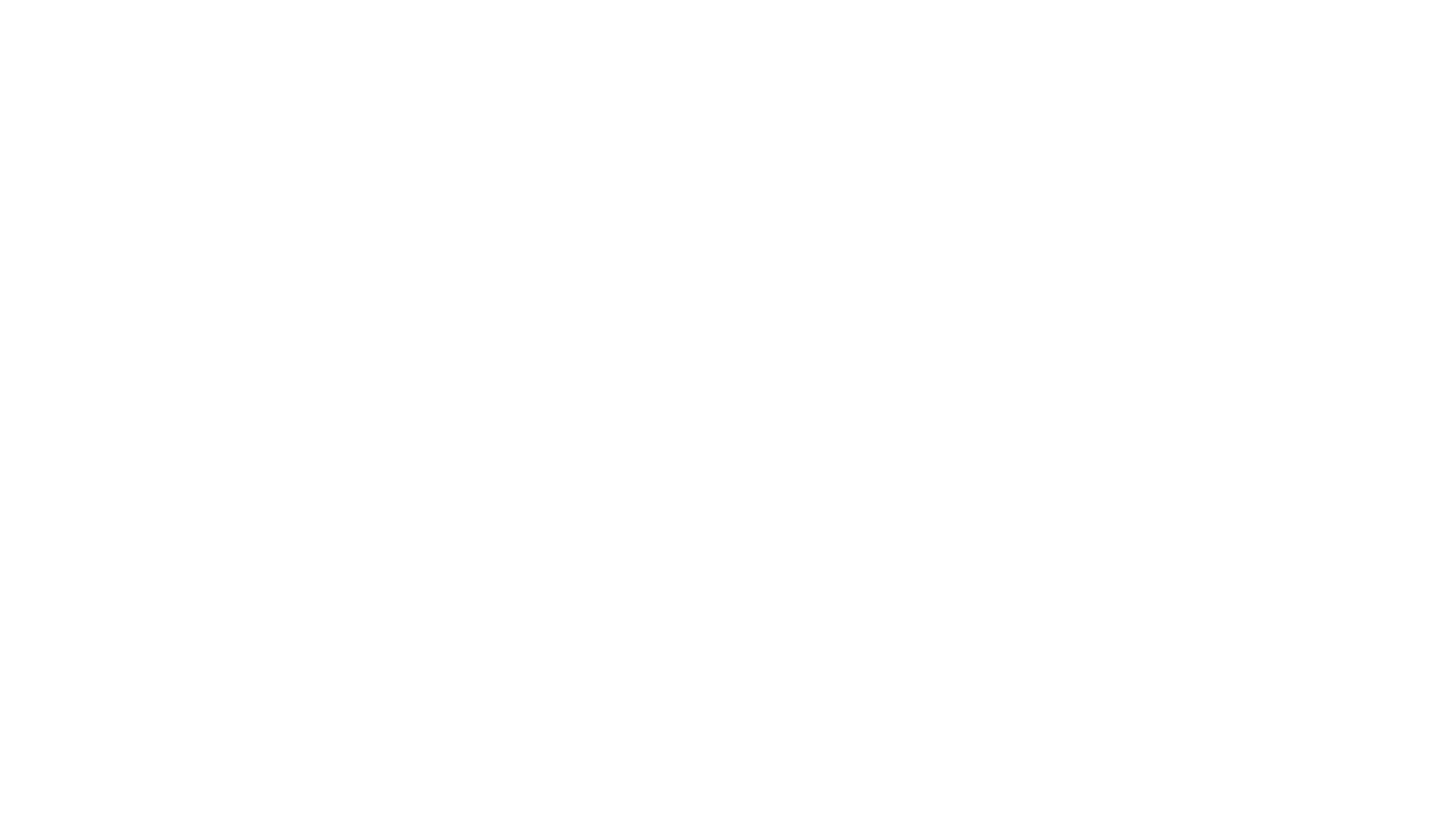