Vaccines
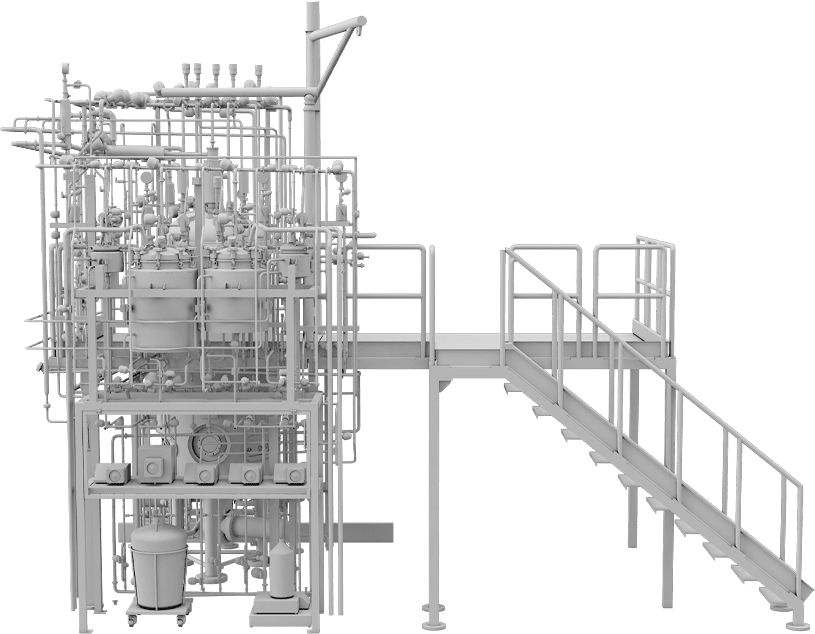
Delicate and tricky biotechnological compounding
-
Peristaltic pumps
Completely aseptic and safe treatment of liquid
-
Seed tanks
Perfect storage of specific strains for upstream processing in the fermenter
-
Utility valves
Complex composition based on URS for an impeccable process
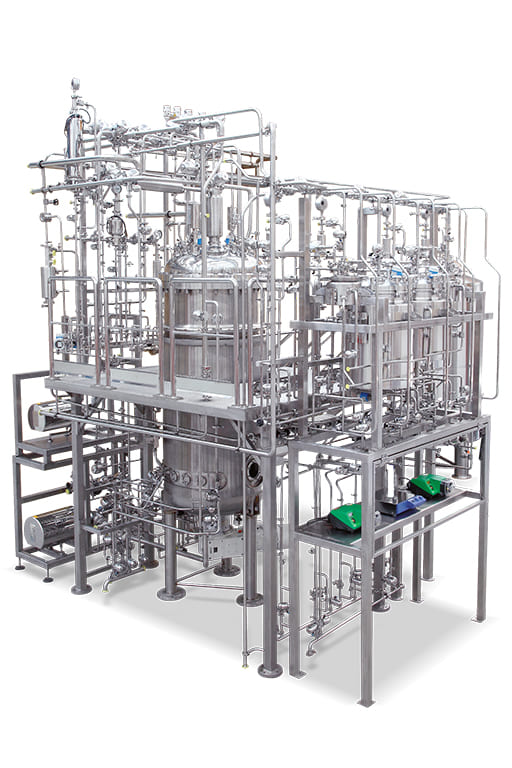
-
Complete Solutions
The fermenter or bioreactor is a pivotal element in industrial production of vaccines. It is indeed a tank which becomes the ideal environment to support the growth of microorganisms.
Cells are able to optimally play their function only under suitable environmental conditions; that’s why it’s essential to constantly monitor parameters such as temperature, pH, gases (oxygen, nitrogen or carbon dioxide), by using sensors and a finely designed automation system.
To keep oxygen concentration stable in aerobic processes, a gas that is not very soluble in water, adds a further layer of complexity: mechanical handling in continuous stirred tanks must be flawless.
Likewise, sterility of the whole process is indispensable.
-
Explore
The design of fermenters is of course compliant with GMP environments, since they’re employed in the Upstream process, that’s to say process to obtain the product for mass production. During Upstream, the culture starts in laboratory with small volume tank, gradually increasing volume of bioreactor itself.
How to choose the right fermenter depends on type, quantity and characteristics of what is to be produced. The fermenter has to be easily sterilizable; with aeration and agitation systems, valves to allow control by sensors.
At the end of fermentation, the process of product recovery, namely Downstream, is carried out: most often the microbial biomass is isolated from the spent culture medium by centrifugation or filtration.
Within the vaccine production cycle, the fermenter is between laboratory cell culture and industrial production, in an intermediate step in the scale-up process.
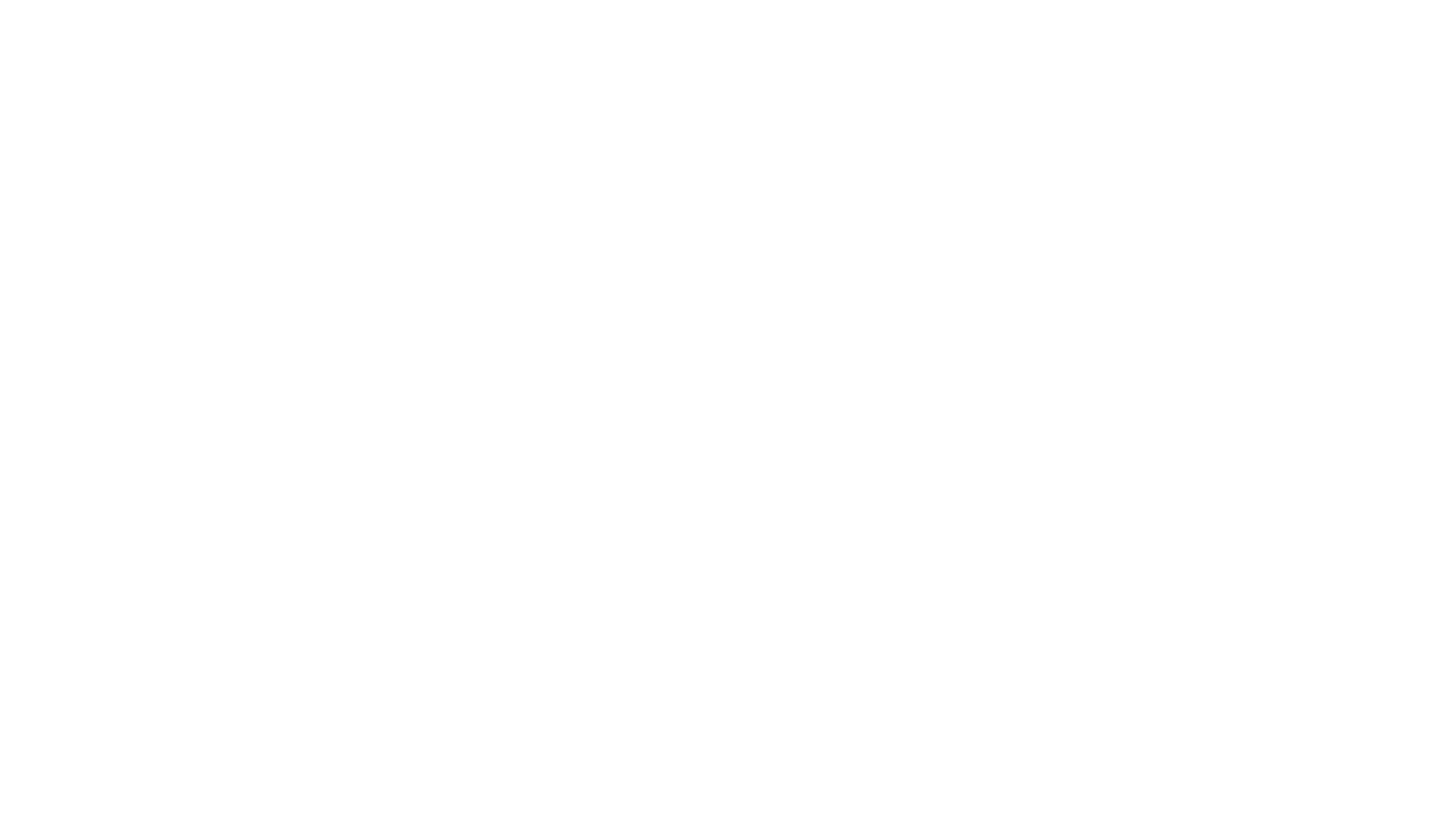